Emulsification and homogenization for toothpaste production
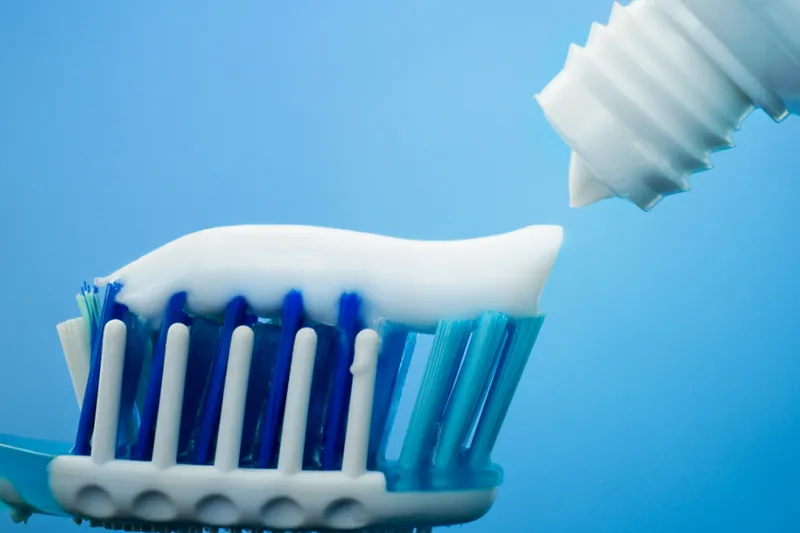
Client Background
A leading toothpaste manufacturer dominating a significant portion of their local market needed to boost production efficiency and improve the emulsification and homogenization processes involving water phases, xanthan gum, abrasives, and surfactants. They sought a solution that would simplify production, maintain strict hygiene standards, and reduce the required production space.
Challenges
One of the main challenges was controlling the particle size distribution during the emulsification of the oil and water phases. Larger particles led to inconsistent texture and color in the toothpaste, and mixing under high-viscosity conditions made it difficult to achieve uniform heat transfer. The precise vacuum control was crucial during the production process to avoid air bubbles in the toothpaste. If the vacuum levels weren’t optimal, the final product would contain air pockets, making it unfit for market standards.
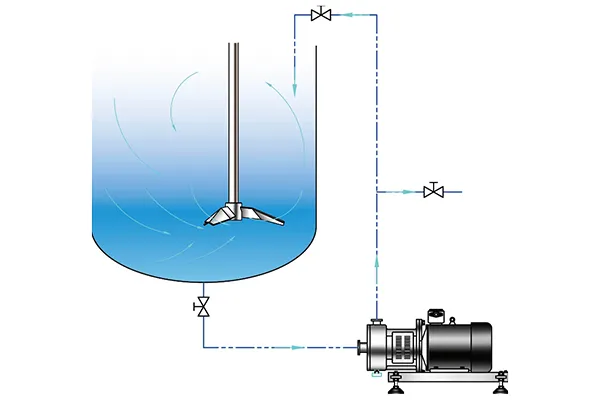
Our Solution
We implemented an inline emulsifier solution, using a dispersing pump to quickly disperse materials into the water phase. This method resolved the challenges of high-viscosity homogenization, and macro-level mixing was achieved through single-axis or coaxial stirring. The vacuum homogenizer was activated, and once the vacuum level reached -0.085Mpa, powder feeding began. When the vacuum level stabilized, just a few minutes of homogenization completed the vacuum emulsification process.
The high-shear emulsification systems by FLUKO deliver efficient, consistent cosmetic and toiletries production, ensuring precise particle distribution and enhanced product stability for chemical manufacturers.