Emulsifying and mixing for the preparation of polymer blends
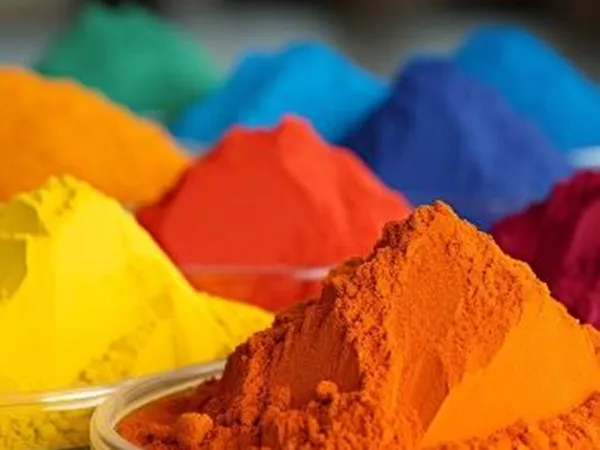
Client Background
The client is a manufacturer of polymer materials, which are based on high molecular weight compounds. Initiators are often required for the raw materials to undergo synthesis and heat processing. Factors such as temperature and pressure can influence the shape and properties of the polymer during the molding process, creating challenges in achieving consistency.
Challenges
One of the challenges faced during the process of polymerization is ensuring a proper seal at high temperatures and vacuum levels, as standard sealing components cannot withstand the conditions. The process requires consistent heat transfer for high-viscosity materials, but very few stirring paddles can meet these demands. The entire preparation process must occur under a high temperature and within a specific pressure range (-0.099 to 0.3 MPa.
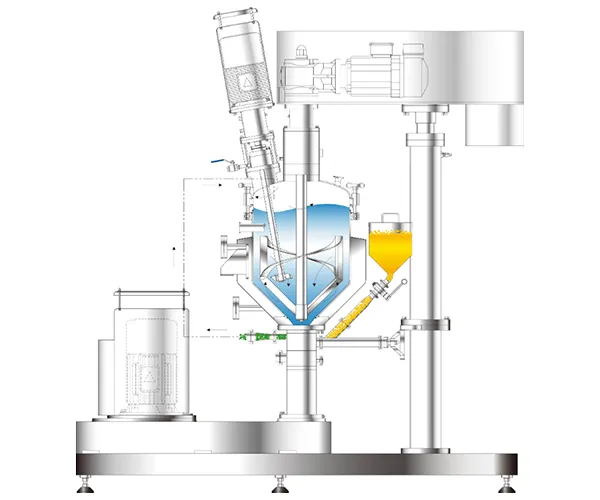
Our Solution
The polymer emulsifying and mixing system by FLUKO offers several unique advantages such as custom-designed mechanical seals tailored to withstand high temperatures and vacuum conditions, ensuring proper sealing throughout the polymerization process. The mixing system also enhances motor cooling capabilities and utilizes specially designed functional agitator paddles to solve the heat transfer challenges associated with high-viscosity materials during the reaction process.
The polymer mixing system by FLUKO ensures precision and reliability under extreme conditions, helping manufacturers efficiently produce high-quality polymer blends while overcoming heat and pressure challenges.